Let’s Set the Scene
A plant facility is completely self-contained — there is minimal risk of any breach of bio-security for any hazardous materials required for processing.
It is designed with the principles of good manufacturing practice in mind and manufacturing processes clearly defined and controlled. All critical processes are validated to ensure consistency and compliance with specifications.
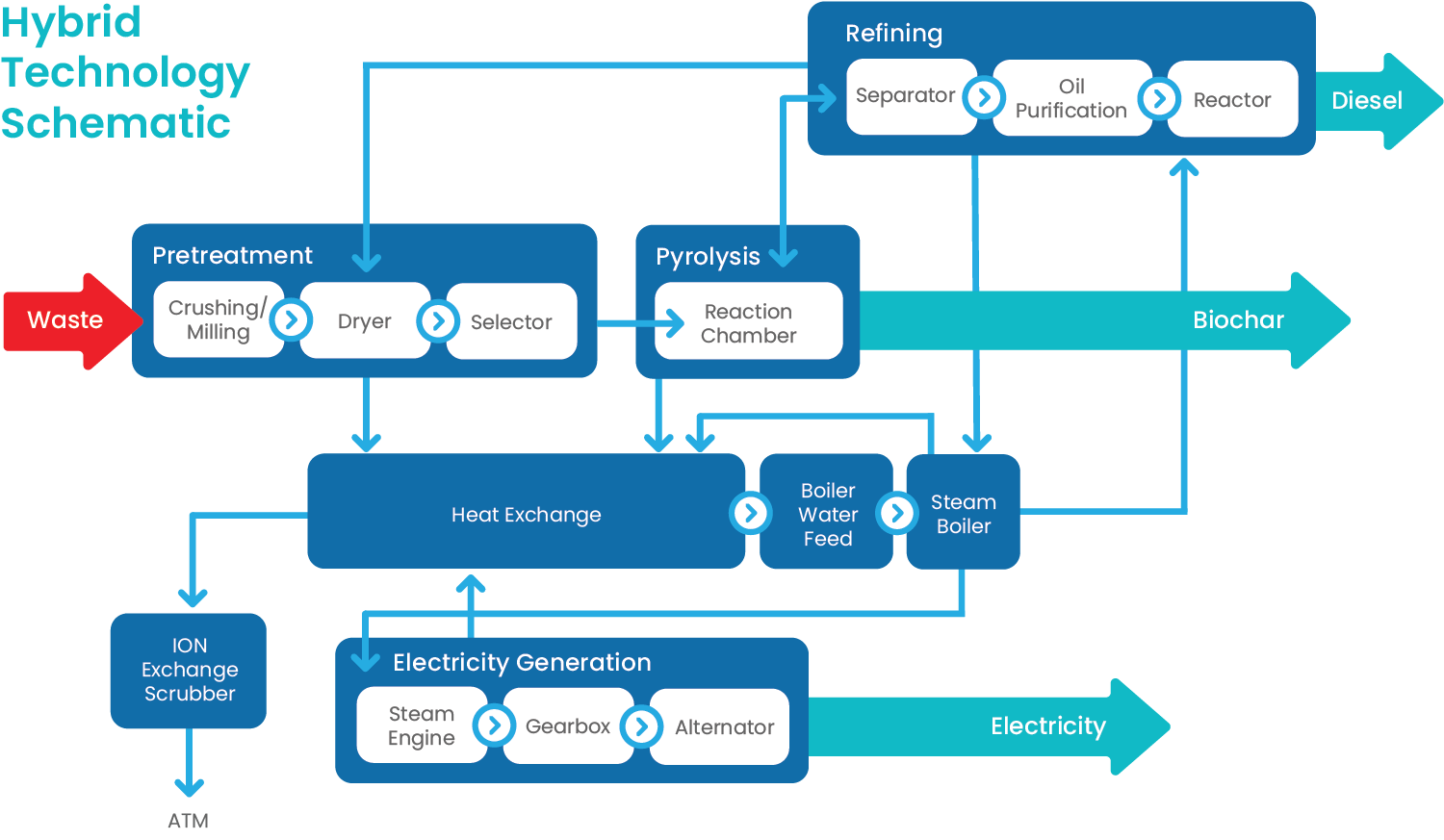
Take a Closer Look
Stage 1:
Delivery and Storage of Waste
In a covered and walled area for deliveries via unloading bays, waste is moved by machinery onto raised conveyors. Non-combustible items are removed using a combination of automatic and manual systems. The conveyor then deposits feedstock into The Shredder.
Stage 2:
The Primary Shredder
This unit consists of an iron core-pulling machine and cuts large material into smaller material. A hydraulically-driven closed-loop system possesses a crushing head, which in turn consists of a shredding type unit capable of shredding up to five tons of material per hour. The system works at very high pressure, and with small displacement, develops exceptional torque.
Stage 3:
The Secondary Shredding Mill and Hopper
From the Primary Shredder, feedstock is broken down into manageable sizes via the Secondary Shredding Mill — a unit comprised of metal cutters and drums specifically designed to cut and mulch waste. The fine output feed is stored in the Hopper, which can be pre-loaded and contains up to ten tons of MSW and other waste. It uses a gravity fed system; a screw mechanism feeds the main pyrolysis unit automatically.
Stage 4:
Pyrolysis Furnace
Our pyrolysis system utilises an initial endothermic, followed by exothermic, reaction processes. Decomposition is achieved in the Pyrolysis Chamber, producing solid, liquid, and gas, by heating at moderately high temperatures under a no-oxygen or low-oxygen atmosphere.
Parameters governing this process include temperature, heating rate, solid residence time, particle size, and density of particles. Our plant furnace operates between 500 – 700ºC with a residence time of approximately thirty minutes, depending on the feedstock used.
Stage 5:
Wet Scrubbers
The pyrolysis mechanisms release hardly any greenhouse gases. However, acidic gases are likely to result and require removal. The Wet Scrubbing unit removes these gases with minimum chemicals by filtering the syngas using a bag filter, and then cooling the exhaust to about 60ºC in a heat exchanger. The exhaust gas then passes through an Acidic Scrubber to remove hydrogen chloride, and an Alkali Scrubber to remove any traces of sulphur dioxide.
Stage 6:
Gas Cooling Tower
Most gasification processes cool syngas to below 500ºC for conventional gas scrubbing. However, this cooling results in significant energy losses. Using our technologies, there is an efficiency advantage in cleaning hot gas and then burning it in a syngas turbine.
The syngas is filtered at an average of 600ºC using sintered metal filters and then burnt in a turbine. By keeping the temperature between 600 – 700ºC, tar condensation is eradicated and the temperature is sufficient to remove alkali metal chlorides.